Flex PCBs, or flexible printed circuit boards, have increasingly become indispensable in modern electronics due to their unique combination of flexibility, durability, and lightweight design. But precisely what are their applications? How do they contrast with traditional rigid PCBs, and what challenges do they pose? This article addresses these inquiries and explores the diverse applications and considerations for flex PCBs.
Flex PCBs are employed in numerous modern electronic applications where space, flexibility, and reliability are crucial. These encompass consumer electronics, wearable devices, medical devices, automotive electronics, and more. They facilitate more compact designs while maintaining high performance.
Understanding the applications of flex PCBs demands delving into their various uses, their distinctions from rigid PCBs, and the trade-offs involved in the utilization of flexible circuits. Let’s explore these domains in greater detail.
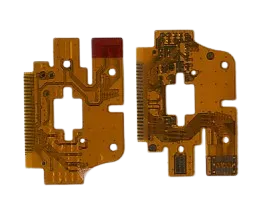
What are Flex PCBs Utilized For?
Flex PCBs are versatile and are utilized across a broad spectrum of applications. They are particularly advantageous when space constraints, weight reduction, and design flexibility are significant factors.
In electronics, flex PCBs are frequently encountered in smartphones, wearables, medical devices, automotive electronics, and aerospace applications. Their flexibility enables them to bend, fold, and twist, making them ideal for products that need to fit into tight or irregular spaces.
Flex PCBs are commonly employed in applications such as:
Smartphones and Tablets: Flex PCBs provide the requisite flexibility to pack components into compact spaces while maintaining functionality.
Wearable Devices: These include health monitors, fitness trackers, and smartwatches, where flexibility is essential for fitting within the device’s curved surfaces.
Medical Devices: Flex circuits are utilized in diagnostic and monitoring equipment, such as pacemakers, hearing aids, and flexible sensors.
Automotive Electronics: From dashboard displays to electric vehicle systems, flex PCBs furnish the necessary flexibility and durability.
Flex PCBs enable manufacturers to create smaller, lighter, and more durable products that would be arduous or impossible to achieve with rigid PCBs.
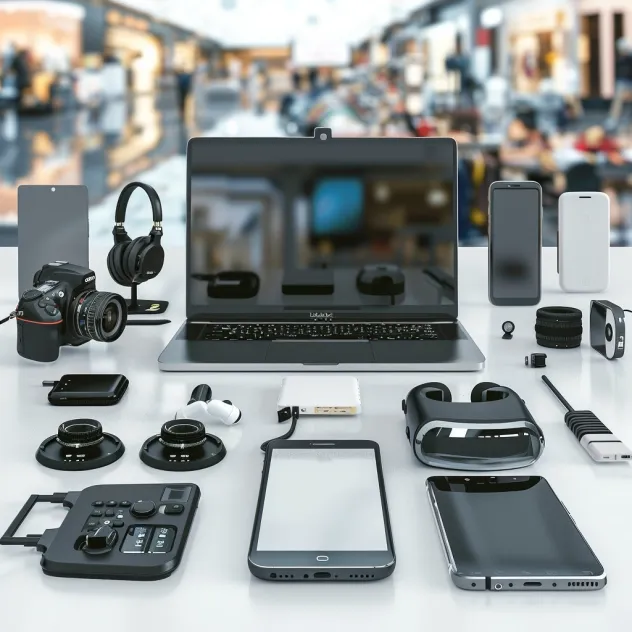
What is the Distinction Between Rigid PCB and Flex PCB?
Rigid PCBs and flex PCBs serve distinct purposes, and the primary disparity lies in their design and physical properties. While both fulfill the same core function—connecting and supporting electronic components—their applications and design requirements are notably different.
Rigid PCBs: These are typically utilized in electronics where the physical layout is fixed, and there is no requirement for bending or flexing. They are fabricated from stiff materials such as fiberglass and are common in products like desktop computers, televisions, and power supplies.
Flex PCBs: In contrast to rigid PCBs, flex circuits are made from thin, flexible materials such as polyimide or polyester. They are ideal for applications where the circuit board must bend or fold, providing greater versatility in product design.
The flexibility of flex PCBs makes them suitable for dynamic and portable applications, whereas rigid PCBs are more appropriate for devices that do not necessitate flexibility.
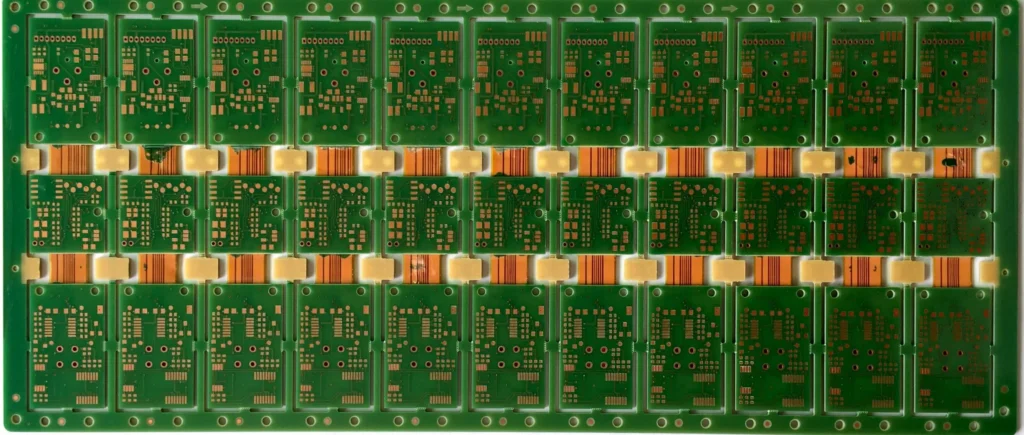
What are the Limitations of Flex PCB?
While flex PCBs offer several benefits, there are also certain limitations that need to be contemplated when choosing between flexible and rigid circuit boards.
Cost: Flex PCBs tend to be more costly than rigid PCBs, mainly due to their more complex manufacturing process.
Durability: Although flex circuits are durable, they are more susceptible to mechanical stress and damage compared to rigid PCBs, especially when exposed to extreme temperatures or harsh environments.
Complexity: Designing a flex PCB demands a higher level of expertise, particularly when it comes to ensuring that the flex circuit can handle repeated bending without damaging the components.
Manufacturing Constraints: The production process for flex circuits is more intricate and requires more specialized equipment and materials, rendering it less suitable for large-scale, mass-production applications.
Despite these challenges, the advantages of flex PCBs—such as their ability to fit into small spaces, their lightweight design, and their capacity to handle complex configurations—often outweigh these limitations, particularly in high-end, space-constrained, or portable applications.
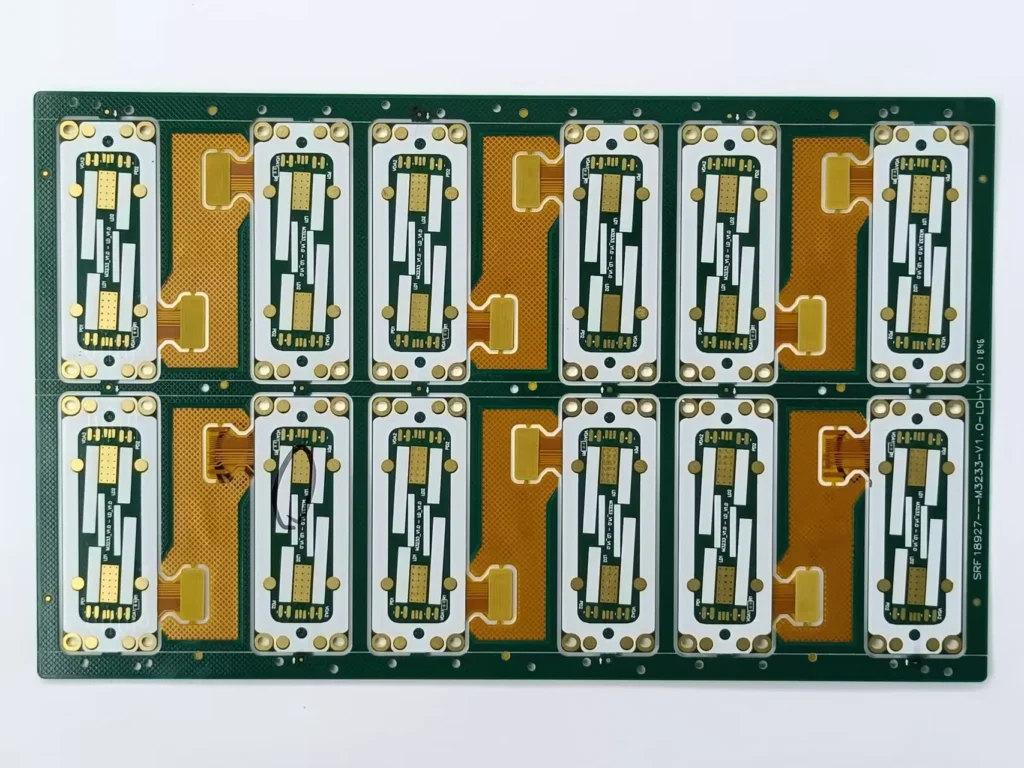
What is the Difference Between Flex PCB and FPC?
While “flex PCB” and “FPC” are terms that are often used interchangeably, they refer to marginally different concepts in the realm of flexible circuit technology.
Flex PCB: This term generally pertains to any printed circuit board fabricated from flexible material. It includes simple single-layer circuits as well as more complex multi-layered structures.
FPC (Flexible Printed Circuit): This term is more specific and typically refers to single-layer flexible circuits used in applications that do not require multiple layers or the complexity of rigid-flex designs.
Both FPCs and flex PCBs serve similar functions in electronic devices, but FPCs are typically smaller, simpler designs utilized in applications like connectors, sensors, and other low-complexity electronics.
Why is Flex Cable Employed?
Flex cables, or flexible cables, are widely utilized in electronics for their capacity to bend and twist while maintaining reliable electrical connections. Their applications are crucial in devices where rigid cables would be impractical due to space or movement constraints.
Flex cables are used in many applications, including:
Wearable Electronics: In devices such as smartwatches, health trackers, and fitness devices, flex cables connect internal components while allowing for movement and bending.
Flexible Displays: Flex cables assist in connecting the display to the rest of the electronic components, particularly in curved or foldable displays.
Medical Equipment: In advanced medical devices, flex cables permit movement within compact enclosures, such as inside a catheter or endoscope.
Flex cables offer substantial advantages when it comes to applications that require a high degree of flexibility without compromising on performance. Their ability to withstand repeated bending and movement makes them an ideal solution in compact and portable devices.
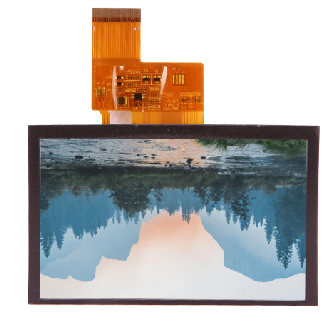
Summary
Flex PCBs are an essential component of modern electronics, offering flexibility and space-saving benefits that traditional rigid PCBs cannot match. While they come with certain limitations, such as higher costs and manufacturing complexity, their applications in consumer electronics, medical devices, and automotive systems render them invaluable. Understanding the difference between flex PCBs and related technologies like FPCs and rigid-flex PCBs can assist manufacturers in choosing the appropriate solution for their designs.